The Most Critical Step in OpenRAMAN
In this post I will share some of the most important tips I learned about optical systems assembly and alignment during my career. I will use OpenRAMAN as a teaching example because applying these tips will make a big difference, as much as going from not working to high quality results. This is typically what the “pros” don’t want you to know so be sure to check it out (true story)!
Let me recall the basic principle of Raman spectroscopy in Figure 1.
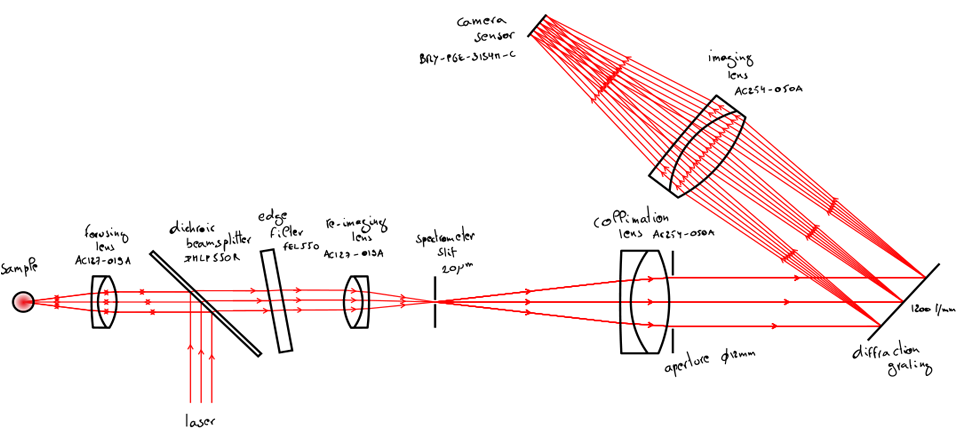
A laser beam is reflected on a dichroic mirror and focused in a tight spot using a focusing lens. The matter in contact with the tight focused laser beam will experience scattering, both normal scattering and Raman (typically 1:109 photons experience Raman scattering). As the light scatters, it goes in all direction and this light is now recollimated using the very same focusing lens, the Raman part passes through the dichroic mirror and is further filtered using an edge pass filter before being re-imaged on a very thin slit using an imaging lens. The slit image is then collimated again, light is dispersed by a grating with different angles which are then re-imaged on a camera sensor using an imaging lens (or machine vision lens). Until now, nothing new – everything is just like what I explained in my previous post on DIY Raman Spectroscopy. The concept was further refined with various updates, but the core principle stayed the same.
This is only a concept-level schematic and in practice you have many effects that comes into play such as stray (undesired) light from ambience or reflections, limited image quality due to aberrations, defects in optical surface (typically on the grating) etc. One of the very first problem you will have to solve as an optical engineer however is the positioning of the elements themselves. Up to now, all optical elements are floating in space at some ideal positions but how do we achieve that in practice and what are the effects of (even tiny) misalignments of the optics?
First, we need to have a look at what happens to an individual lens subject to misalignment. Let’s have a look of the two common errors in Figure 2: tilt and decenter. The figure shows both the effect of image location through the tracing of 3 rays but also the effect on image quality through the wavefront plots. By the way, this is the AC127-019-A lens that I’m using aplenty in the spectrometer.
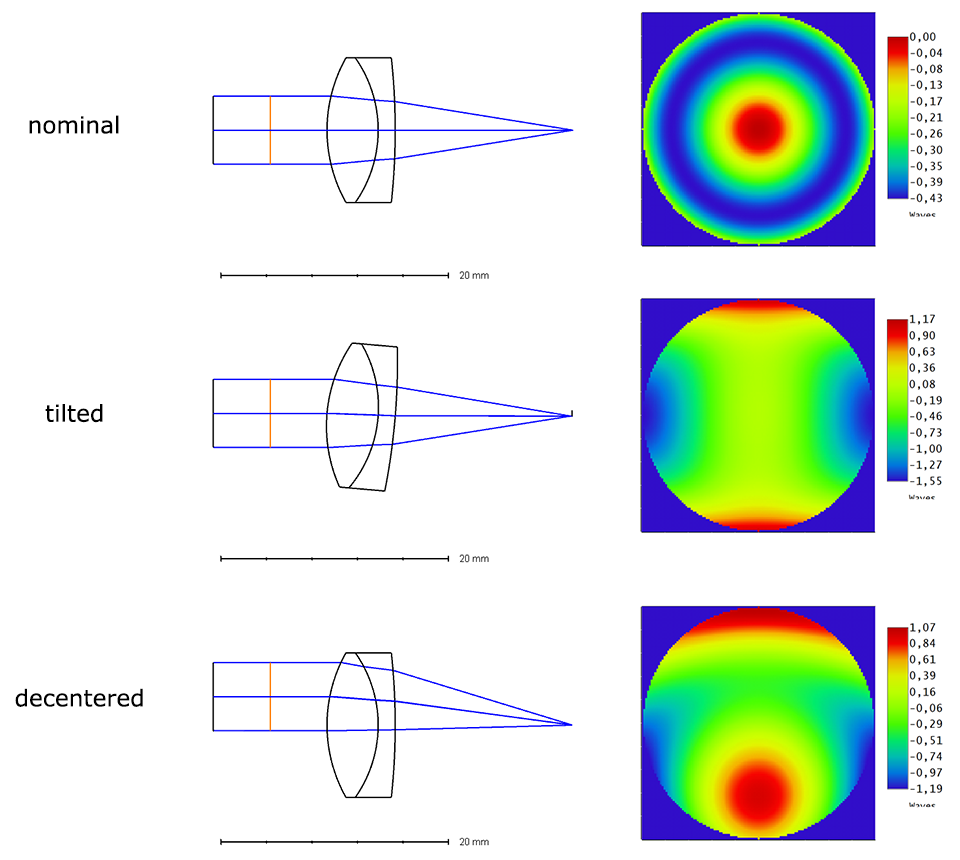
The nominal case gives the reference case. Here, everything is well centered to the incoming collimated beam. The image is formed on the lens mechanical axis which is coincident with the optical axis. Note that even if we are in the perfect case, we still have some remaining spherical aberration. This is perfectly normal for an achromatic doublet such as this one to have some remaining spherochromatism.
In the tilted case, the mechanical axis of the lens does not coincide with the optical axis of the beam although the light still strikes the lens in its center region. The main effect of the tilt is to introduce a lateral shift in the image position. This is something normal and desirable because you can see this case as a tilted beam striking a centered lens. It is because we have this lateral shift that our spectrometer manages to resolve the spectra thanks to the grating changing the tilt angle of the beam depending on the incoming wavelengths. Note that a tilted beam is known to produce coma and astigmatism which will reduce the image quality. The wavefront plot clearly shows predominant astigmatism here.
Finally, the decentered case has more subtle effects. Here the two axes (lens and beam) are still parallel but are offset to each other such that the rays strike the lens with non-symmetrical angles. Because of the loss of symmetry, more complex aberrations appears but the general effect is to reduce image quality. At stronger decenters, some of the incoming light rays will even be clipped by the lens limited dimensions! Note however that the image position did not change (apart from the effects of the aberrations) compared to the nominal case.
This is for collimated beam but remember that the front part of our spectrometer takes the scattered light to produce a collimated beam using the first lens and that the second lens then re-image the bright scattered spot onto the slit using a second lens. This is a re-imaging system, and it suffers the same problems of decenter and tilts. Using the first lens as coordinated system reference, we have the various possibilities depicted in Figure 3.
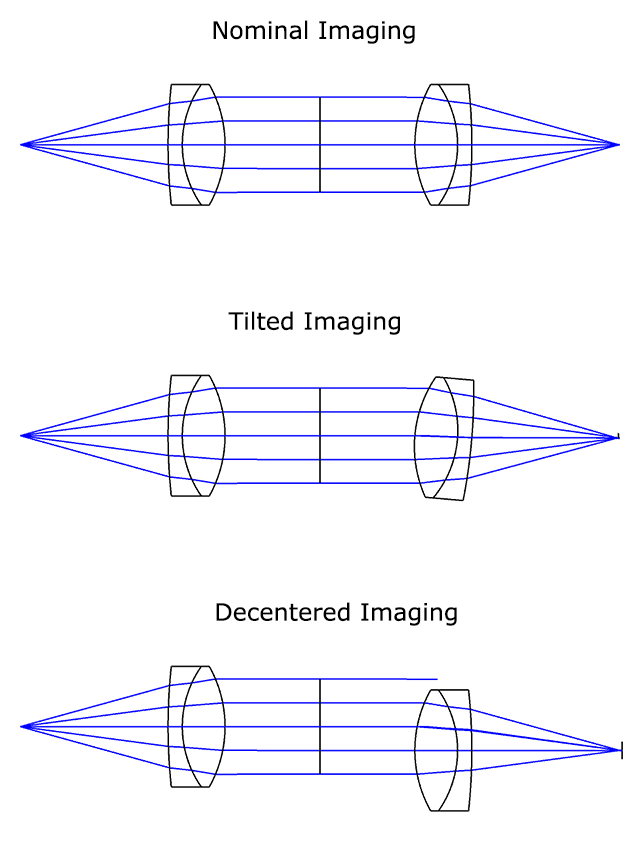
The same conclusions as for a single lens applies. A tilt will shift the spot image position and a decenter will vignette rays. Both modes will also produce a loss of spot image quality but here we don’t care so much because we’re already collecting a blurry laser spot in the first place so it’s more a question of energy transfer and image location. If you wonder why we get a blurry spot in the first place and not a tight, sharp, laser spot, think of Raman in a liquid (or even a diffuse solid) as a volumetric effect that is sensitive to the illumination density. As you get closer to the spot center (both laterally and in depth), the illumination density increases and so the Raman emission increases as well so you’re actually imaging a Raman emission volume with the brightest part being at the laser spot location. Also, here I considered that the stop of the system (what limits the rays opening in the plots) is the diameter of the first lens. In practice the light will reach the edge of the lenses and produce some stray light due to weird reflections but, again, we’re not looking into image quality here but only in light collection.
Clearly, in this aspect, a decenter is not acceptable because we will loose light and reduce our spectrometer efficiency. A tilt has even worse effect because we are shifting the image location. Remember that on the image (right-handed) side we have a very narrow slit to filter the light! A 1° shift will displace the beam by 330 µm, more than ten times the size of our slit in the Performance Edition! No need to mention that if the light does not strike right through the clear aperture of the slit it will be completely clipped and we will have zero energy transfer so zero signal on the spectrometer.
The question is now, how do we achieve good centering and low tilts when we assemble/design an optical system?
Usually, the answer is concentricity. By machining parts that are concentric you can already guide them and avoid strong decenters. Typically, placing lenses in a tube will avoid decentering of more than the gap between the lens outer diameter and the tube inner diameter. Even better, by using a sharp lip and a retainer ring it is also possible to reduce tilt as well by forcing the optical center of the lens to coincide with the mechanical axis of the tube.
Figure 4 shows Thorlabs’s AC127-019-A-ML mounted lens. You can spot: (1) the lens, (2) the mount, and, (3) the retainer ring. The square lip of the mount presses on the round surface of the lens as the retainer ring is screwed in place which forces the lens optical axis to align with the mechanical axis of the part. Using this procedure, you can achieve decenters as low as 50 µm and tilts on the order of 0.05°. This is the standard mounting procedure of lenses but there exist many variations of this concept.
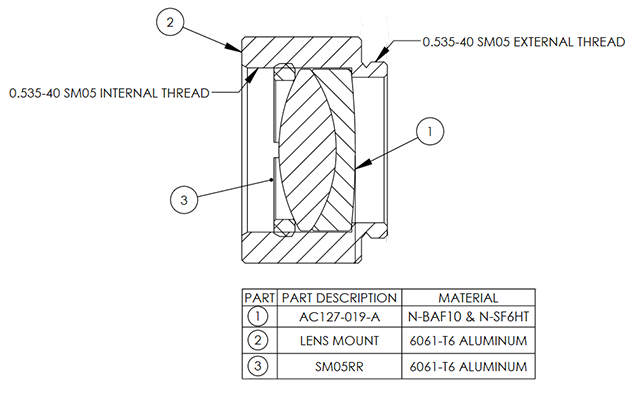
Once you have two lenses like this, you can screw them into both ends of a tube. The flat end side of the tube will be forced to match the flat side of the mount and control the overall tilt.
In OpenRAMAN, I did not use a tube but rather a cage system. This is shown in Figure 5.
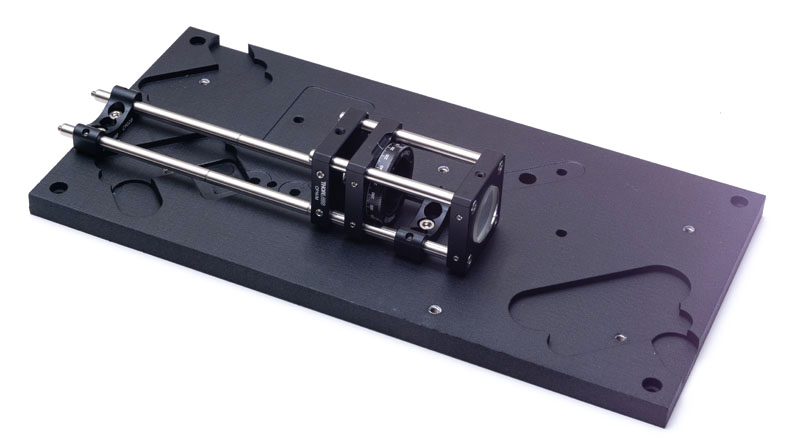
Although the system looks more complex, the overall idea is the same. Thorlabs provides machined parts with high precision which have four holes that are concentric elements to elements and allow the control of tilt and decenters through the usage of stainless-steel bars. The trick here was to use extra long bars to ensure that the mechanical axis of the part on the left-hand side of the picture was aligned with the mechanical axis of the part on the right-hand side. Once the two subgroups are firmly fixed using fasteners on the base plate, we can remove these alignment rods and still have a very good alignment of the cuvette part and the lens/slit part on the other side. If we did not, we were likely to have both strong tilt and decenter of the two subgroups because the gap of the screws will typically allow tilts of up to ~3° and the large leverage between the two subgroups can transform this tilt to a decenter of up to ~5 mm.
Note that even with the small tilt produced by this system, we still don’t have the guarantee that the light will strike on the clear aperture part of the slit. First, the remaining tilt might not be completely negligible but, most of all, we have no guarantee that the slit itself is centered on the expected image position! The slit mount has a typical gap of ~100 µm compared to the cage system mount and, even worse, after enquiring Thorlabs, they cannot guarantee that the slit itself is centered in its mount. They mentioned a (probably conservative) ±1 mm tolerance.
So, in any case, we need some sort of tuning mechanism to center the laser spot image on the slit. Fortunately, we can use the dichroic mirror itself to shift the image location. This is shown in Figure 6.
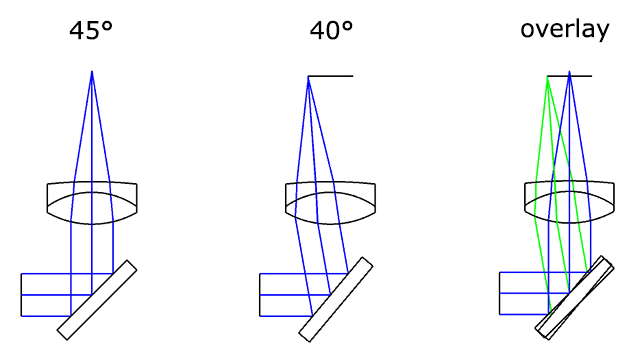
Figure 6 shows the effect of a dichroic mirror positioned at 45° (nominal) and at 40° (tilted). The two configurations are also compared on an overlay.
It is relatively clear that a very small tilt of the dichroic mirror will produce a strong shift of the laser spot. For this reason, a kinematic base with fine angular adjustment such as Thorlabs KM100 is required.
Because we are using a slit, we should only care of the horizontal tilt and not the vertical because the slit is much taller than it is wide (typically >2 mm compared to ~20 µm). This is something that is often overlooked in OpenRAMAN but that was actually a deliberate choice to simplify alignment. Indeed, most spectrometers rely on optical fibers to transfer the Raman signal to the spectrometer but injecting the light into a fiber requires aligning in both the horizontal and vertical directions which is much more difficult to achieve, especially with small core fibers. In OpenRAMAN, because we’re not using a fiber, we only have one degree of freedom which is extremely easy in terms of alignment. This was done on purpose and was based on my experience with light coupling in single-mode fibers.
If you have followed our alignment video (near ~51:00), you have seen that I’m using the red curve in the spectrometer program to tune the dichroic mirror. This curve is directly proportional to the light reaching the sensor and by using it I can easily identify when the laser spot image is well centered on the slit.
Again, however, we have made an idealized version of the dichroic mirror in Figure 6. For the same reason as previously, we have no guarantee that the initial beam will not be tilted or decentered for the very same reasons because the KM100 kinematic bases are mounted using a screw itself (same for the laser mount) which does not guarantee at all the orientation and position.
For the lenses, we relied on concentricity to achieve a good initial starting point. When folding the beam, things get a bit more difficult. The usual way to deal with folded beams is to have a two-mirror configuration to alter both the decentering and the tilt of the beam. This is the reason a second mirror has been inserted in the OpenRAMAN setup.
The mechanism is shown in Figure 7 with various tilt angles.

Although the two mirrors are usually not completely decoupled, the first mirror allows to tune the decentering of the beam while the second one allows to tune the tilt. In practice, it is often necessary to play back and forth between the two until an optimum is found.
But because we now have two mirrors that have some tuning capabilities, we need a way to adjust them such that we sufficiently close to the nominal case. In OpenRAMAN, this is achieved using concentricity again with the two frosted disk as shown in Figure 8.
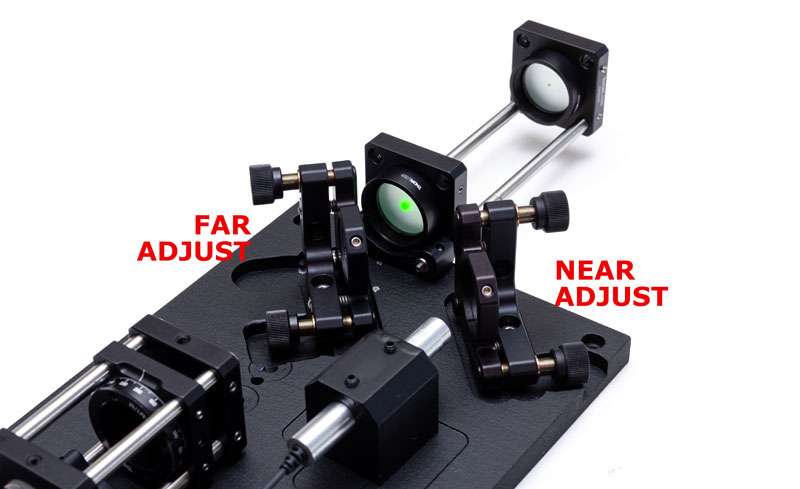
The frosted disks have a hole in their centers, and, thanks to the cage system, are concentric with the optical axis of the slit imaging system. By making the laser beam passes through both holes, we know that the axis of the laser beam will be almost equal to the mechanical axis of the system which is itself very close to the optical axis of the slit imaging system. It will not be perfect, but it will be much closer than what we could have achieved by hand positioning. Also, the last step will be to fine tune the dichroic mirror angle using the spectrometer software such that we can bring the laser spot image right onto the actual slit clear aperture.
This is what I consider as the most critical aspect in OpenRAMAN and it is the reason that makes it works. As you have seen, none of it happened by accident – it is all deliberate choices on how to perform the alignment of the various system axis. To align an OpenRAMAN successfully, it is primordial to understand these aspects and their consequences.
Also, this is where you see the difference between experimented and non-experimented optical engineers. An experimental optical engineer will always construct a system with easiness of alignment in mind. Poor, or inexperienced engineers, will stick to the vision of the nominal design and will not orient the conception to a friendly alignment device. This is something that is also exacerbated by the division of labors between the optical designers, the system engineers, the mechanical engineer and the person in charge of the MAIT. Every person will only conduct work according to his/her own challenge and few will take the time to think harder to make the life of the next person easier. This is something that I observed quite often and would like to fight through my work in the #DevOptical series.
Before I conclude this post, there are two remaining points that I would like to address.
First, the dichroic mirror and the edge pass filter will produce a lateral shift in the beam which will limit the energy transfer in the system due to vignetting. This effect can be cancelled by including a compensation window. Since I already covered this topic in a previous post, I will not repeat it again. I however encourage you to re-read the corresponding section of that post now that you have a better understanding of the effect of decenters.
The second point concerns Thorlabs cage system components. I must confess that although I love the cage system concepts due to its reduction in the number of degrees of freedom to cover tilt and decenters, I’m not a big fan of their lens mounts.
A typical 1” lens mount of Thorlabs is the CP35 (or CP35/M for the metric version), which is shown in Figure 9.
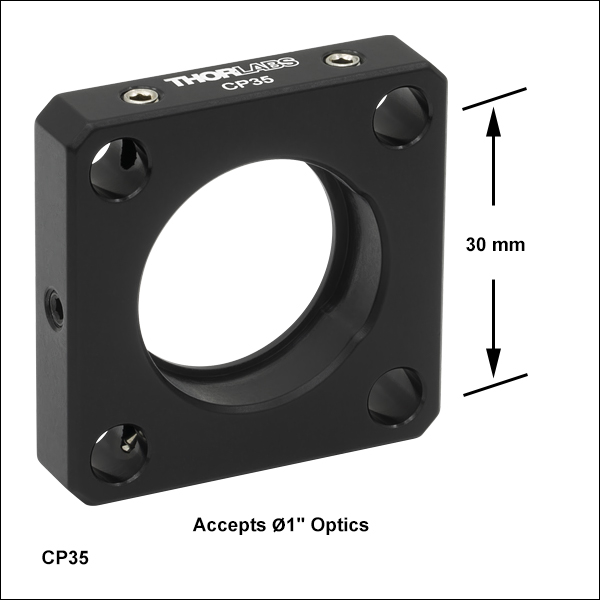
These mounts work using a set screw that you can see on the left-hand side part of the picture. A nylon-tipped set-screw presses on the outer diameter of the lens until it contacts the edges on the right-hand side of the picture.
Not only is this terrible in terms of resistance to shock and vibration during transports, it also breaks an important rule in lens mounting which is to never use the outer diameter of the lens as a mounting reference. Mounting a lens through its mechanical outer diameter is a terrible practice that affects the tilt and decenter of the lens. In comparison, the square-lip mounting of Figure 4 is known to be at least one order more precise in tilt and decenter.
Also, these mounts (CP35-like) have a huge gap between their inner mechanical diameter and the lens outer diameter so in practice the decenter is even worse than that. On larger, 2 inches, version, I have even seen thick lenses like the ACT508-100-A completely tilt in the mount as pressure is put on the set-screw! This is a disaster in terms of optical performances as we often struggle with the aberrations induced by tilts smaller than 0.1°…
There is unfortunately not much alternative to this day to lens mounting in cage system from Thorlabs. If you machine your own parts, a system such as the one in Figure 4 will be much more reliable in both optical performances and resistance during transport. This is an important thing to keep in mind when working with Thorlabs part. I hope they will provide an alternative someday. Note that the CP14 we use aplenty in the spectrometer to hold the AC127-019-A lenses has the exact same problem. I would like to give a big thanks to Young, Samuel, Mehmet, Arif, James, Lilith, Vaclav, Hitesh,Jesse, Sivaraman, Jon, Sebastian,Eric, Themulticaster, Cory, Karel, Alex, and Marcel who have supported this post through Patreon. I also take the occasion to invite you to donate through Patreon, even as little as $1. I cannot stress it more, you can really help me to post more content and make more experiments!
0 Comments